Introduction
Uchida Co., Ltd. has been molding and processing composite materials (FRP) since establishment in 1968. Our business focuses on advancing the distinctive “lightweight, strong, and non-corrosive” characteristics of CFRP to deliver new potential in next-generation mobility and weight reductions. In this issue, we will be exploring CFRP molding processing from a specialist manufacturing standpoint.
What is Carbon? Delving into CFRPs
While the term carbon fiber refers to thin strands of carbon, these fiber strands will not retain their form on their own. Thus, they are combined with a resin to retain the shape and maximize its distinct lightweight and strong characteristics.
Composite materials are substances composed of two or more constituents, such as carbon fiber and resin, to yield new functions. Carbon fiber reinforced plastic (CFRP) is the name given to a composite created from carbon fiber and resin.
The composite is named after the type of fiber employed. Carbon fiber composites are named carbon-fiber reinforced plastic (CFRP), glass fiber composites are referred to as GFRP, and aramid fiber composites are called AFRP. The distinctive “lightweight, strong, non-corrosive” qualities of advanced CFRP has opened doorways for leading-edge development in various fields, such as aviation, satellites, automobiles, and sporting and leisure equipment industries. Unlike metals and other isotropic materials, with CFRP, the strength is determined by the orientation of the carbon fibers (anisotropic) and therefore necessitates product-specific material design. The high degree of design versatility, in terms of resin and carbon-fiber constitution and arrangement, means that is volatile and difficult-to-handle without expert technical knowledge of the material and its properties.
Challenges
Despite its numerous merits, CFRP is still succumbs to various challenges in productivity and cost-efficiency. These include the need for molds, high material costs, and complex production processes.
CFRP Molding Methods
Before delving into CFRP processing, let’s first look at molding methods. There is a wide variety of CFRP molding methods which are selected according to the desired application, shape/form, and production lot.
Autoclave Molding
RTM (Resin Transfer Molding)
Va-RTM (Vacuum Assisted Resin Transfer Molding)
Press Molding
Hand Lay-up Molding
Filament Winding Molding
Sheet Winding Molding
Pultrusion
3D Printer
At Uchida, we use the fabrication methods shown in red.
Autoclave Molding Method: The Hallmark of High-quality CFRP Product Manufacturing
Despite the extensive range of molding methods, autoclave molding remains the hallmark method for design versatility and high-quality CFRP fabrication. High-quality CFRP created using the autoclave molding method is known as dry carbon. This method is suitable for prototyping and small-lot production as it does not require expensive metal molds. The diagram below illustrates the production process of CFRP products using the autoclave molding method.
Autoclave CFRP Parts Manufacturing Process
Image of overheating and pressurization inside the device
Uchida’s Commitment to CFRP Lamination and Molding
Uchida Lamination Room
The Lamination Room is the “silver bullet” for the CFRP quality. In other words, it is the core center for mold processing and key deciding factor in quality. Here the carbon sheets (prepregs) are cut, laminated, vacuum-bagged, and autoclaved. It is the center of the line in our one-stop manufacturing which delivers everything from design and analysis through to mold fabrication lamination, molding, secondary processing, painting/coating, final inspection, and testing.
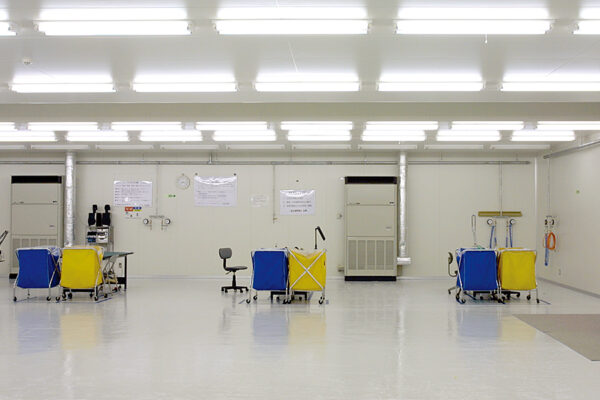
JIS B 9920 cleanliness class maximum concentration (Pcs/m³) / Class 5 : 100,000m³ / Capacity : m² (16,000×16,000mm) 760m² (16,000×16,000×3,000mm) / Temperature and humidity condition : Temperature : 23℃±3℃, Humidity 65% less / Ambient conditions : Temperature 35℃ during summer, Humidity 70% less / Ambient conditions : Temperature 35℃ during summer, Humidity 70% less / Temperature -5℃ during winter, Humidity 40% less
Commitment to Engineering Management and Controls
The CFRP sheets (prepregs) processed in the Lamination Room have a use-by-date like that of food, and generally requires storage in temperatures of 18℃ or below. The handling of prepregs drastically impacts the quality, requiring meticulous management and traceability of material exposure times and temperature/humidity levels from the time of removal from the freezer to cutting, lamination, vacuum-bagging, and autoclaving. Regardless of how proficiently our technicians perform the work, if the proper engineering management and controls aren’t put in place, then major defects may arise down the track after molding.
The lamination process involves layering ultra-fine carbon sheets of 0.2mm, to form a laminate stack, and is a key determining factor for strength and rigidity. Thus, any shortcomings in engineering controls risk impacting the structural integrity, causing internal defects which are not detectable with external inspection. Such processes whereby defects cannot be detected down the track are referred to as “focused processes.” During lamination, multiple cross-checks are performed by technicians and inspectors to confirm the correct fiber orientation and ensure against human errors such as failure to remove protective films, preventing defects before they occur.
Commitment to CFRP Laminating Technology
Uchida heralds honed experience in all fields from compact items to large scale monolithic products. The type of prepregs, resin, and fibers used, and the ease-of-application for each material will vary drastically depending on the use environment. As such, our focus remains on manufacturing that is based on honed knowledge of product structures and material-specific properties, alongside continuous efforts to minimize post-production processes.
We take pride in our unique fine-tuned techniques and complex laminate molding technologies born from our origins in mannequin manufacturing. To see these technologies in action, we urge you to check out our Carbone Mirai, featured below, which was created to commemorate 45 years of developments since our establishment.
How to make the CARBONE MIRAI with carbon fiber
CFRP Processing (CFRP Machining)
There are some important points to note when machining CFRP.
Knowledge of its Anisotropic Structure (Fiber Orientation)
As a review, CFRP is an anisotropic material whose strength depends on the direction of the fibers. Thus, machining requires a specific understanding of the fiber orientation, lamination structure, and properties of the resin used as the matrix. Proper machining paths cannot be created without unique know-how on CFRP (composite material) handling and property variances, such as differences in machining resistance depending on the amount and orientation of the fibers, laminate configuration, or differing thermal properties contingent on the resin.
Dry Processing Prerequisites
Cutting oils are incompatible with CFRP machining due microscopic liquid-absorbing properties of the carbon fibers which soak up and retains the oils if immersed. Although moisture absorption is not visible on the exterior, as any soaked surfaces may delaminate after long-term use of the product, we must exercise caution when handling the material. If using the products in humid environments, we will specially treat the surface with paint or sealant after machining to prevent moisture absorption.
Uchida’s Commitment to Carbon Processing
Uchida Tool and Jig Room
The Jig and Tool Room is the center (department) for CFRP processing. Here we design and manufacture molding dies, inspection or adhesive jigs, and other tools used for CFRP molding in our machining center, alongside secondary processing of CFRP products after molding. At Uchida, we offer one-stop services ranging from design and analysis to mold fabrication, laminate molding, secondary processing, coating, inspection, and testing. And our Jig and Tool Room oversees getting the entire manufacturing process rolling.
Commitment to Molding
For CFRP products, while mold processing is an important and quality-critical process, the most fundamental step is the designing of the mold. The mold determines the quality of the product.
At Uchida, our proficiency in large complex and monolithic molded products combined with extensive experience across diverse fields allows us to accommodate even the most difficult requests. We are further leveraging our strengths in one-stop manufacturing to produce “easy-to-use” molds that cater to downstream or post-processing processes. An easy-to-use mold is designed and processed to best match the production quantity and mold materials, based on an understanding of the product structure, while delivering effortless stacking, marginal temperature irregularities, minimal breakage during handling, and easy handling capacities. The most essential element in molding is an adept understanding of the entire manufacturing process.
Commitment to CFRP Machining
While we say CFRP machining, the item often employs a different internal material. Many of the CFRP products we manufacture are complex structural items with foam or metal inserts at the time of molding. In machining, we conduct prior investigations for (1) understanding CFRP anisotropy and resin, and (2) CFRP parts composited with metal, to determine the optimal machining method. Even the most complex composite product, such as the above, machine processing is generally performed dry. At Uchida, we possess vast experience in drilling, thread tapping, trimming, and 3D-shape machining, and employ a wide range of tools based on specific knowledge of CFRP’s characteristics.
Uchida’s Commitment to Secondary Processing
Uchida Finishing Room
The Finishing Room is where the finishing processes of molded CFRP products are completed. This includes applying finishing coats to machined molds and other final post-molding processes such as trimming, drilling, gluing, assembling, and painting/coating. This room oversees the final finishing steps in our one-stop manufacturing service which delivers everything from design/analysis and mold fabrication to lamination, molding, secondary processing, painting/coating, final inspection, and testing.
Commitment to Mold Finishing
For CFRP-use molds (prototype molds, in this case), a resin coating is applied to the surface of the mold after it has been precision machined in the machining center. Technically speaking, any mold machined in a machining center will have an uneven surface due to the use of ball end mills and similar. The accuracy of the mold’s surface is transferred directly to the CFRP product and, therefore, we must pay careful attention to process the surface with the final appearance in mind.
This step can completely change the quality in appearance of the product, so we are continuously working to refine mold quality without compromising the precision of the machining center.
Commitment to CFRP Product Finishing
At Uchida, our main business lies in prototype development and high-mix low-volume production. Secondary processing in the machining center is limited to products which require high dimension precision, processing of bulky structures, or CFRP/metal hybrid co-processing. Aside from this, secondary processing is generally completed by hand in the finishing room.
Due to manufacturing complexity and the costs of CFRP materials, any errors in final stages can lead to significant losses. With our key focus in quality, we are adamant about cultivating a refined eye for detecting defects in the front-end processes, and on augmenting the skills of our technicians and production environment to prevent any defects in our meticulously crafted products.
Summary
In this issue, we delved further into Uchida’s CFRP manufacturing technologies. The creation of high-quality products from CFRP parts relies on a harmonious and systematic fusion of facilities, environment, and human technology. Uchida boasts history (experience) + ample facilities/environment + commitment from our technicians.
If you are considering product fabrication, we urge you to seek a manufacturer who is well-versed and has a proven record in CFRP.
Related useful contents
You can explore related content by clicking on a topic of interest.
ABOUT UCHIDA - 55 years since our founding
We leverage a wealth of technical expertise as a CFRP molding and processing manufacturer using FRP, GFRP, and CFRP materials. We offer a one-stop solution, encompassing design, analysis, manufacturing, secondary processing, assembly, painting, quality assurance, and testing.
UCHIDA's equipment
We have cutting-edge equipment to ensure that we can address even the most advanced challenges of our customers.
Video Library
In the following video, we provide a detailed overview of our manufacturing process. Please feel free to watch and learn more.
ピンバック: 【コラム】GFRPとは? | 株式会社UCHIDA
ピンバック: 【コラム】コンポジット・カーボンコンポジット『CFRP』とは? | 株式会社UCHIDA
ピンバック: 【コラム】複合材料 メリット デメリット | 株式会社UCHIDA
ピンバック: 【コラム】軽量化手法『FRP・GFRP・CFRP』 | 株式会社UCHIDA
ピンバック: 【コラム】PCM製法とは? CFRP | 株式会社UCHIDA
ピンバック: 【コラム】ドライカーボン『CFRP』とは? | 株式会社UCHIDA
ピンバック: 【コラム】FRP・GFRP・CFRP 切削加工・機械加工 | 株式会社UCHIDA
ピンバック: 【コラム】FRP・GFRP・CFRP 短納期に対応 | 株式会社UCHIDA
ピンバック: 【コラム】炭素繊維強化プラスチック成形『CFRP』 | 株式会社UCHIDA
ピンバック: 複合材料 メリット デメリット【コラム】 | 株式会社UCHIDA
ピンバック: GFRPとは?【コラム】 | 株式会社UCHIDA