Introduction
These days, jargon such as carbon fiber, carbon fiber reinforced plastic, CFRP, and composites appear in a myriad of situations. Here, we will discuss the differences between PAN-based and Pitch-based carbon fiber.
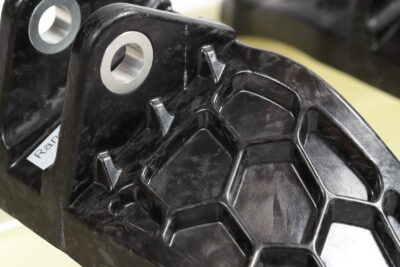
Overview
Carbon fiber is broadly classified into two types according to the base materials used for production. The carbon fiber itself cannot retain form on its own and, because of its high specific strength (strength-to-weight ratio), is often composited with a plastic polymer such as epoxy resin and used as a Carbon Fiber Reinforced Plastic (CFRP).
PAN-based Carbon Fiber
PAN-based (poly-acrylonitrile) carbon fiber is produced from acrylonitrile via a process of PAN fiber synthesis, flame retardant treatment, carbonization, graphitization, surface treatment, and sizing. The lightweight and high-strength characteristics of PAN-based carbon fiber have led to its widespread use in structural components for automobiles, aircraft, and other applications. PAN-based carbon fiber accounts for most of the carbon fiber on the market.
Pitch-based Carbon Fiber
Pitch-based carbon fiber is produced from coal, petroleum, and coal tar by-products (pitch) through a series of carbonization, surface treatment, and sizing processes at high temperatures. It has a high modulus of elasticity, high thermal conductivity, extremely low thermal expansion, is lightweight, and highly rigid. Pitch-based carbon is mainly used for industrial robot arms, artificial satellite components, and other similar applications.

Summary
This issue details the differences between PAN-based and pitch-based carbon fiber, offering a clearer insight into varying properties and applications. While each exhibits differing characteristics, the manufacturing method for both types of carbon fiber will equally vary depending on the application, shape, and other factors.
Related useful contents
You can explore related content by clicking on a topic of interest.
ABOUT UCHIDA - 55 years since our founding
We leverage a wealth of technical expertise as a CFRP molding and processing manufacturer using FRP, GFRP, and CFRP materials. We offer a one-stop solution, encompassing design, analysis, manufacturing, secondary processing, assembly, painting, quality assurance, and testing.
We have cutting-edge equipment to ensure that we can address even the most advanced challenges of our customers.
DMG森精機 - VS1000/40/2050
X軸:2,050mm(ストローク) / Y軸:1,000mm / Z軸:600mm / テーブル作業面:2,250×1,000mm
ASHIDA MFG Co., Ltd.
Autoclave Oven 2
Size : Ø1,150x1,000mm / Operating temperature : at normal temperature - 400℃ / Design pressure : 2.0Mpa (maximum working pressure) / Vacuum system : back suction system / Vacuum units : 5
ASHIDA MFG Co., Ltd.
Autoclave Oven 3
Size : Ø3,000x6,000mm / Operating temperature : at normal temperature - 200℃ / Distribution accuracy : ±2.5℃less / Heating rate : 4.0℃/min. (empty furnace) / Cooling rate : 4.0℃/min. (empty furnace) / Design pressure : 0.99Mpa (maximum working pressure) / Working pressure : 0.7Mpa less (if no specification from the manufacuturer 0.3Mpa around) / Pressure accuracy : ±0.02Mpa(for pressure setting of 0 - 0.99Mpa/cm²) / Boost pressure accuracy : 0 - 0.03Mpa/min / Pressure source : compressed air (regular use) / Vacuum system : back suction system / Vacuum units : 10
Oven
Size : W1,000xH1,000xD1,000mm / Temperature range : Environmental Temperature +20 - 300℃ / Temperature elevation capability : Environmental Temperature (20 - 40℃) - 300℃ / 45min less / Vacuum system : back suction system / Vacuum units : 10
ESPEC CORP.
Temperature & Humidity Chamber
INSTRON
Static Universal Testing Machine 5985
Oven
Size : W7,000xH3,000xD2,000mm / Temperature range : Environmental Temperature +20 - 300℃ (Max) / Temperature elevation capability : Environmental Temperature (20 - 40℃) - 300℃ / 60min less / Vacuum system : back suction system / Vacuum units : 10
NEO
X axis : 4,000mm (stroke) / Y axis : 2,000mm / Z axis : 1,200mm / C axis : 0° - ±270° / B axis : 0° - ±110° / Table working place : 4,000x2,000mm
【開発】
3Dプリンター | Markforged
Painting booth
Various painting, and clear finish is done in dedicated painting booth
Adhesion, Finishing, Coating Room
Finishing process, such as trimming, drilling, and bonding, surface treatment of the molded product type and is done in a private booth
Toshiba Matrixeye EX (Ultrasonic flaw detector)
Matrix-Arrey : 32
AMETEK CREAFORM Metra
SCAN750 Elite (3D scan)
Olympus Corp.
Inverted Microscopes
Oven
Size : W450xH450xD450mm / Temperature range : Environmental Temperature +20 - 650℃ / Temperature elevation capability : Environmental Temperature+50 - 650℃/120min less
Cutting Plotter Table working place : W1,500xL3,500mm
SHIMA SEIKI MFG., LTD
Cutting Plotter
Krauss Maffei
Epoxy resin injection machine Resin 60L / Hardener 25L
Krauss Maffei
630t Press machine Height total 5,200mm / Length max 1,500mm / Width max 1,200mm / Whole cycle time per component part 240sec
DMG森精機 - NV5000B/40
X軸:1,020mm(ストローク) / Y軸:510mm / Z軸:510mm / テーブル作業面:1,320×600mm
Big sized clean room
JIS B 9920 cleanliness class maximum concentration (Pcs/m³) / Class 5 : 100,000m³ / Capacity : m² (16,000x16,000mm) 760m² (16,000x16,000x3,000mm) / Temperature and humidity condition : Temperature : 23℃±3℃, Humidity 65% less / Ambient conditions : Temperature 35℃ during summer, Humidity 70% less / Ambient conditions : Temperature 35℃ during summer, Humidity 70% less / Temperature -5℃ during winter, Humidity 40% less
CAD / CAM
CATIA V5 : 2 / THINK DESIGN : 1 / MASTER CAM : 4 / Other 3D/CAD : 3 / Other 2D/CAD : 5
In the following video, we provide a detailed overview of our manufacturing process. Please feel free to watch and learn more.
ピンバック: 炭素繊維 特徴【コラム】 | 株式会社UCHIDA
ピンバック: FRP・グラスファイバーの違い【コラム】 | 株式会社UCHIDA
ピンバック: 繊維強化プラスチック『FRP・CFRP』とは?【コラム】 | 株式会社UCHIDA