Introduction
Uchida has been molding and processing composite materials (FRP) since its establishment in 1968. Our business centers on paving new pathways in next-generation mobility and weight reduction through the advancement of CFRP and its distinctive “lightweight, strong, and non-corrosive” characteristics. In this issue, we will discuss CFRP lamination and molding technologies from the perspective of a specialist manufacturer–our perspective.
What is Carbon? Delving into CFRPs
While the term carbon fiber refers to thin strands of carbon, these fiber strands will not retain their form on their own. Thus, they are combined with a resin to retain the shape and maximize its distinct lightweight and strong characteristics.
Composite materials are substances composed of two or more constituents, such as carbon fiber and resin, to yield new functions. Carbon fiber reinforced plastic (CFRP) is the name given to a composite created from carbon fiber and resin.
The composite is named after the type of fiber employed. Carbon fiber composites are named carbon-fiber reinforced plastic (CFRP), glass fiber composites are referred to as GFRP, and aramid fiber composites are called AFRP. The distinctive “lightweight, strong, non-corrosive” qualities of advanced CFRP has opened doorways for leading-edge development in various fields, such as aviation, satellites, automobiles, and sporting and leisure equipment industries. Unlike metals and other isotropic materials, with CFRP, the strength is determined by the orientation of the carbon fibers (anisotropic) and therefore necessitates product-specific material design. The high degree of design versatility, in terms of resin and carbon-fiber constitution and arrangement, means that is volatile and difficult-to-handle without expert technical knowledge of the material and its properties.
Challenges
Despite its numerous merits, CFRP is still succumbs to various challenges in productivity and cost-efficiency. These include the need for molds, high material costs, and complex production processes.
CFRP Molding Methods
Before delving into CFRP processing, let’s first look at molding methods. CFRP molding methods come in varying forms and are selected according to the application, shape/form, and production lot.
Autoclave Molding
RTM (Resin Transfer Molding)
Va-RTM (Vacuum Assisted Resin Transfer Molding)
Press Molding
Hand Lay-up Molding
Filament Winding Molding
Sheet Winding Molding
Pultrusion
3D Printer
At Uchida, we use the fabrication methods shown in red.
Autoclave Molding Method: The Hallmark of High-quality CFRP Product Manufacturing
Despite the extensive range of molding methods, autoclave molding remains the hallmark method for design versatility and high-quality CFRP fabrication. High-quality CFRP created using the autoclave molding method is known as dry carbon. This method is suitable for prototyping and small-lot production as it does not require expensive metal molds. The diagram below illustrates the production process of CFRP products using the autoclave molding method.
Uchida’s Commitment to CFRP Lamination and Molding
Uchida Lamination Room
The Lamination Room is the “silver bullet” for the CFRP quality. In other words, it is the core center for mold processing and key deciding factor in quality. Here the carbon sheets (prepregs) are cut, laminated, vacuum-bagged, and autoclaved. It is the center of the line in our one-stop manufacturing which delivers everything from design and analysis through to mold fabrication lamination, molding, secondary processing, painting/coating, final inspection, and testing.
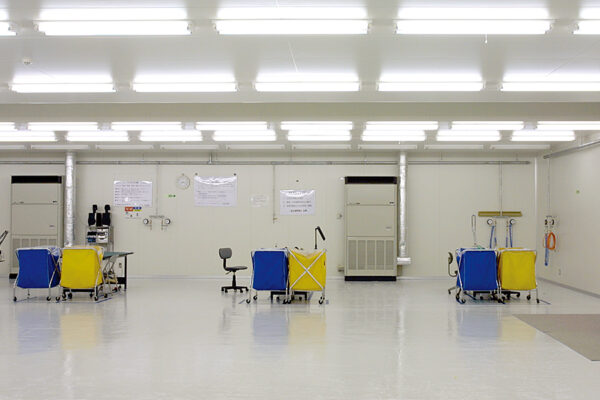
JIS B 9920 cleanliness class maximum concentration (Pcs/m³) / Class 5 : 100,000m³ / Capacity : m² (16,000×16,000mm) 760m² (16,000×16,000×3,000mm) / Temperature and humidity condition : Temperature : 23℃±3℃, Humidity 65% less / Ambient conditions : Temperature 35℃ during summer, Humidity 70% less / Ambient conditions : Temperature 35℃ during summer, Humidity 70% less / Temperature -5℃ during winter, Humidity 40% less
Commitment to Engineering Management and Controls
The CFRP sheets (prepregs) processed in the Lamination Room have a use-by-date like that of food, and generally requires storage in temperatures of 18℃ or below. The handling of prepregs drastically impacts the quality, requiring meticulous management and traceability of material exposure times and temperature/humidity levels from the time of removal from the freezer to cutting, lamination, vacuum-bagging, and autoclaving. Regardless of how proficiently our technicians perform the work, if the proper engineering management and controls aren’t put in place, then major defects may arise down the track after molding.
The lamination process involves layering ultra-fine carbon sheets of 0.2mm, to form a laminate stack, and is a key determining factor for strength and rigidity. Thus, any shortcomings in engineering controls risk impacting the structural integrity, causing internal defects which are not detectable with external inspection. Such processes whereby defects cannot be detected down the track are referred to as “focused processes.” During lamination, multiple cross-checks are performed by technicians and inspectors to confirm the correct fiber orientation and ensure against human errors such as failure to remove protective films, preventing defects before they occur.
Commitment to CFRP Laminating Technology
Uchida heralds honed experience in all fields from compact items to large scale monolithic products. The type of prepregs, resin, and fibers used, and the ease-of-application for each material will vary drastically depending on the use environment. As such, our focus remains on manufacturing that is based on honed knowledge of product structures and material-specific properties, alongside continuous efforts to minimize post-production processes.
We take pride in our unique fine-tuned techniques and complex laminate molding technologies born from our origins in mannequin manufacturing. To see these technologies in action, we urge you to check out our Carbone Mirai, featured below, which was created to commemorate 45 years of developments since our establishment.
How to make the CARBONE MIRAI with carbon fiber
Summary
In this issue, we detailed CFRP molding technology, starting with an overview of CFRP manufacturing. Engineering management is a central component in CFRP mold processing which demands a strictly temperature and humidity controlled clean room and freezer storage of materials. Accumulated knowledge and experience are paramount when advising on complex shapes and structures and, therefore, if you are considering product fabrication, we urge you to seek a manufacturer who is well-versed and has a proven record in CFRP.
Related useful contents
You can explore related content by clicking on a topic of interest.
ABOUT UCHIDA - 55 years since our founding
We leverage a wealth of technical expertise as a CFRP molding and processing manufacturer using FRP, GFRP, and CFRP materials. We offer a one-stop solution, encompassing design, analysis, manufacturing, secondary processing, assembly, painting, quality assurance, and testing.
UCHIDA's equipment
We have cutting-edge equipment to ensure that we can address even the most advanced challenges of our customers.
Video Library
In the following video, we provide a detailed overview of our manufacturing process. Please feel free to watch and learn more.
ピンバック: 【コラム】GFRPとは? | 株式会社UCHIDA
ピンバック: 【コラム】PCM製法とは? CFRP | 株式会社UCHIDA
ピンバック: 【コラム】オーブン成形とは? CFRP | 株式会社UCHIDA
ピンバック: 【コラム】炭素繊維とカーボンの違いについて | 株式会社UCHIDA
ピンバック: 【コラム】カーボン オートクレーブ温度 | 株式会社UCHIDA
ピンバック: 【コラム】軽量化のメリット『FRP・GFRP・CFRP』 | 株式会社UCHIDA
ピンバック: 【コラム】GFRPガラスエポキシ | 株式会社UCHIDA
ピンバック: 【コラム】FRP・GFRP・CFRPの違いについて | 株式会社UCHIDA
ピンバック: 【コラム】炭素繊維PAN系とピッチ系の違い『CFRP』 | 株式会社UCHIDA
ピンバック: 炭素繊維PAN系とピッチ系の違い『CFRP』【コラム】 | 株式会社UCHIDA
ピンバック: GFRPガラスエポキシ【コラム】 | 株式会社UCHIDA