Introduction
Since our establishment in 1968, Uchida has been pursuing new frontiers in composite (FRP) manufacturing with a focus on leveraging the “strong, lightweight, and non-corrosive” characteristics of CFRP toward next-generational mobility and weight reductions. In this issue, we will discuss prepreg lamination from our perspective as a specialist in the field.
What is CFRP? A Deeper Look at Carbon Fiber Reinforced Plastics
As per the name CFRP (carbon fiber reinforced plastic) is a composite material (type of FRP) whereby a plastic polymer base material is fortified with carbon fibers. The resulting distinctive “lightweight, strong and non-corrosive” qualities has made CFRP a leading material-of-choice across diverse industries and applications.
Carbon fiber itself is a fine yarn-like filament which exhibits exceptional strength but is unable to hold a form on its own. With the product known as CFRP or dry carbon, we composite these strength-obtaining carbon fibers with a plastic polymer to achieve a strong, highly elastic, and formable material.
CFRP Molding Methods
Before delving into CFRP processing, let’s first look at molding methods. There is a wide variety of CFRP molding methods which are selected according to the desired application, shape/form, and production lot.
CFRP Molding Methods
Autoclave Molding
RTM (Resin Transfer Molding)
Va-RTM (Vacuum Assisted Resin Transfer Molding)
Press Molding
Hand Lay-up Molding
Filament Winding Molding
Sheet Winding Molding
Pultrusion
3D Printer
At Uchida, we use the fabrication methods shown in red.
Autoclave Molding Method: The Hallmark of High-quality CFRP Product Manufacturing
Despite the extensive range of molding methods, autoclave molding remains the hallmark method for design versatility and high-quality CFRP fabrication. High-quality CFRP created from carbon prepregs using the autoclave molding method is known as dry carbon. This method is suitable for prototyping and small-lot production as it does not require expensive metal molds.
The diagram below illustrates the production process of CFRP products using the autoclave molding method.
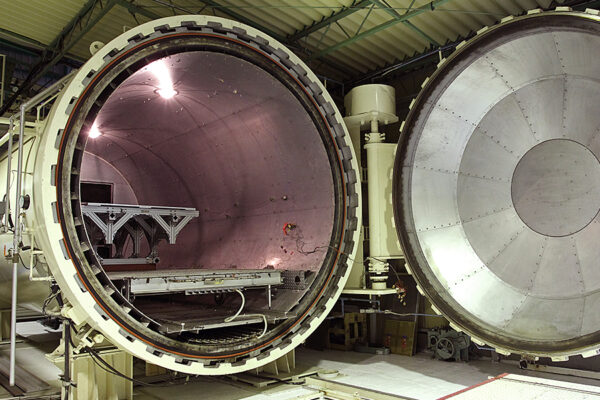
Autoclave Oven 3
Size : Ø3,000×6,000mm / Operating temperature : at normal temperature – 200℃ / Distribution accuracy : ±2.5℃less / Heating rate : 4.0℃/min. (empty furnace) / Cooling rate : 4.0℃/min. (empty furnace) / Design pressure : 0.99Mpa (maximum working pressure) / Working pressure : 0.7Mpa less (if no specification from the manufacuturer 0.3Mpa around) / Pressure accuracy : ±0.02Mpa(for pressure setting of 0 – 0.99Mpa/cm²) / Boost pressure accuracy : 0 – 0.03Mpa/min / Pressure source : compressed air (regular use) / Vacuum system : back suction system / Vacuum units : 10
What are Prepregs?
The term prepreg refers to a carbon fiber sheet that is pre-impregnated with resin.
Reinforcing carbon fibers that are pre-impregnated with resin prior to curing are typically referred to as carbon prepregs.
Intermediary base material prior to molding (pre-cured)
Prepreg Lamination
Video on carbon prepreg lamination
Matters of Caution When Laminating
・Make sure to remove the protective film and backing paper.
→ Results post-molding defects.
・As an anisotropic material*, lamination of fiber reinforced plastics and CFRPs must strictly follow the design specification, fiber orientation, sequence, and vacuum degassing processes set out in the product design instructions.
→ While appearing identical with the same thickness, the final product will have vastly different mechanical properties.
→ Mistakes in lamination sequence may result in defects and deformations.
・Take care when laminating curved surfaces to prevent the fibers from wrinkling.
→ Cause defects such as uneven or changes in thickness after post-molding.
・Perform lamination in a clean room and take care to prevent any contaminates or foreign objects from mixing between the layers.
→ Lead to defects.
*An anisotropic material is a material whereby the strength of the material is determined by the orientation of the fibers.
Quasi-isotropic Lamination (Lay-up)
As an anisotropic material, carbon fiber reinforced plastics can be designed to exhibit the required strength in the required direction. Quasi-isotropic lamination (lay-up) is technique that orientates the fibers to achieve equal strength in all directions to simulate the isotropic properties seen in metals and other isotropic materials; hence the name quasi-isotropic.
Summary
In this issue, we covered the lamination of prepregs used as intermediate materials in CFRP manufacturing. Hopefully this has given you a clearer insight into the processes and choices involved.
Related useful contents
You can explore related content by clicking on a topic of interest.
ABOUT UCHIDA - 55 years since our founding
We leverage a wealth of technical expertise as a CFRP molding and processing manufacturer using FRP, GFRP, and CFRP materials. We offer a one-stop solution, encompassing design, analysis, manufacturing, secondary processing, assembly, painting, quality assurance, and testing.
UCHIDA's equipment
We have cutting-edge equipment to ensure that we can address even the most advanced challenges of our customers.
Video Library
In the following video, we provide a detailed overview of our manufacturing process. Please feel free to watch and learn more.